Why Floor Insulation Is a Game Changer for Cold Climate Homes
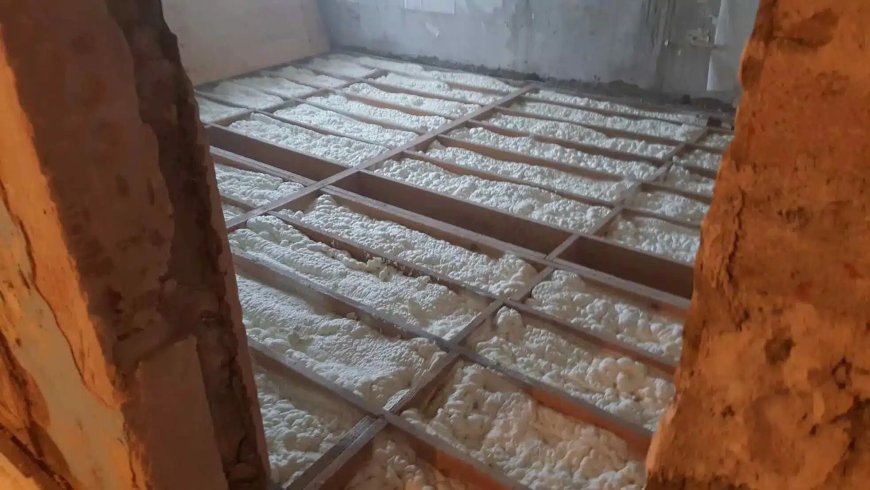
In a cold-climate house, as much as 15 % of total heat loss seeps straight through uninsulated floors, second only to attic losses. Adding floor Insulation contractor creates an immediate thermal break, blocking drafts, stabilizing indoor temperatures, and cutting heating bills by 10–25 % in the first year. It also stops under‐floor condensation, which can rot joists and warp finished flooring.
Put simply, insulating the floor keeps the warmth you pay for inside your living zone instead of letting it drain into the crawl space or slab. The payoff begins on day one in comfort and continues for decades in reduced energy demand and extended building lifespan.
This guide delivers everything you need—from materials and performance data to installation methods and decision factors—to make an informed, confident choice about floor insulation for cold environments.
How Floor Insulation Works
Heat flows from warm to cold until a barrier stops it. A well-installed layer of underfloor insulation delivers three key functions:
-
Resistance (R-value) to reduce conductive heat loss. Higher R-values block more heat trying to escape
-
Air sealing prevents convective drafts sneaking between boards—especially critical during windier days
-
Moisture control, keeping humid indoor air from meeting cold surfaces below the dew point and causing dampness or rot
Floor insulation differs from wall or attic insulation because it must resist foot traffic, potential moisture, and vibration. Effective options buffer heat while maintaining structural integrity and comfort.
Material Options Compared
Material |
R‑value per 25 mm (1 in) |
Installed thickness for R‑25 |
Water Resistance |
Compressive Strength |
DIY‑friendliness |
Typical Cost (USD/m²) |
Mineral wool batts |
4.3 |
150 mm |
Good |
Low |
Moderate |
6–8 |
High‑density fiberglass batts |
3.7 |
175 mm |
Fair |
Low |
High |
4–6 |
Expanded polystyrene (EPS) panels |
4.0 |
160 mm |
Moderate |
Moderate |
High |
7–9 |
Extruded polystyrene (XPS) boards |
5.0 |
125 mm |
High |
High |
High |
9–12 |
Polyisocyanurate (ISO) boards |
6.0 |
100 mm |
High |
High |
Moderate |
11–14 |
Closed‑cell spray foam |
6.5 |
100 mm |
Excellent |
N/A (adheres in place) |
Low (specialist) |
18–25 |
Bonus tip 1: Where crawl-space headroom is limited, selecting rigid foam floor insulation such as XPS or ISO compresses high R-value into less thickness, guaranteeing long-term performance without sagging.
Each material balances R-value, moisture control, cost, and ease-of-installation. For example, batts are budget-friendly and easy to fit, but may compress or settle; rigid boards resist water and support loads, while spray foam seals air and resists moisture completely, though it requires professional application and higher cost.
Technical Performance Data
Parameter |
Uninsulated Wood Floor |
R‑25 Insulated Floor (XPS) |
Improvement |
Design heat loss (W/m²·K) |
0.74 |
0.17 |
77 % less |
Mean surface temperature at –10 °C outdoor / 21 °C indoor |
13 °C |
18 °C |
+5 °C warmer underfoot |
Winter condensation risk on joists |
High |
Near-zero |
Eliminated |
Annual heating energy use for 150 m² house (kWh) |
19 500 |
15 000 |
–4 500 kWh (~23 %) |
(Market data sourced from 2023–2024 cold-climate studies in Canada and Scandinavia.)
Bonus tip 2: Use thermal floor insulation in tandem with an airtight, vapor‑permeable membrane on the warm side. This boosts drying potential while obstructing moisture flow.
These data points validate why underfloor insulation is not merely a comfort upgrade—it’s a financially sound investment with measurable returns.
Installation Approaches
Above‑joist retrofit
Remove the existing subfloor, install insulation boards or batts above joists, then reinstall sheathing
Ideal when updating floor finishes or replacing existing decks. Provides easy access to full insulation layers, but can raise the floor height slightly
Between‑joist retrofit
Staple batts or apply spray foam from beneath (crawl space or basement)
Insulating floor joists here is less disruptive inside living spaces but may require sealing joists and blocking air flow between cavities
Continuous rigid layer under screed or slab
Typically used for basement floor insulation in new builds or renovation projects
Serves dual roles: thermal barrier + capillary break (prevents moisture rising through concrete)
Helps level uneven slabs and boosts efficiency of heated concrete floors
Bonus tip 3: For cold floor solutions above an unconditioned garage, apply a hybrid method—spray foam for air sealing, topped with fiberglass or mineral wool batts to moderate costs and maintain vapor permeability.
Things to Consider Before Making a Decision
Factor |
Why It Matters |
Climate zone & design temperature |
Must achieve R‑25 to R‑30 in sub-zero zones for effective insulation |
Ventilation strategy |
Conditioned crawl spaces handle rigid or spray foam better; vented spaces need vapor‑open membranes |
Moisture history |
Past leaks call for closed-cell foam or XPS to protect from damp |
Floor access & occupancy |
Spray foam requires temporary vacating; batts allow staged installation |
Assess your climate, ventilation setup, moisture records, occupancy patterns, and budget. This ensures you match performance goals with long-term comfort and cost savings.
Common Questions
Does floor insulation make rooms feel warmer fast?
Yes. Raising floor surface temperature by just 3 °C improves radiant comfort so rooms feel 1–2 °C warmer, often without adjusting the thermostat.
Can I combine under‑floor heating with insulation?
Absolutely. Placing insulation beneath radiant heating pipes ensures heat travels upward, improving efficiency by 15–20 %.
Will added thickness raise finished floors?
Not if you install insulation under joists. For above‑joist retrofits, you’ll need to plan for door thresholds and trim height changes.
Do I need a vapor barrier?
In cold climates, a smart vapor retarder (Class II/III) on the warm side prevents moisture buildup, while still allowing drying toward the cooler side.
How do I know when to call in a specialist?
If dealing with complex venting, potential moisture intrusion, or using spray foams, rely on experts for airtight sealing and correct method.
FAQ
What R‑value do floors need in extreme cold regions?
Aim for R‑25 to R‑30. Anything lower risks condensation and increases payback periods.
Is spray foam always the best option?
Not always. Closed-cell foam is excellent for air sealing and moisture resistance, but rigid boards match thermal performance while having lower embodied carbon and general handling safety.
Does mineral wool last under a ventilated crawl space?
Yes—as long as it remains dry and supported, mineral wool can hold its R‑value for 30+ years without notable drop-off.
Can I DIY rigid board installation?
Absolutely. Just plan for tight fitting, tape every seam properly, and always wear eye and respiratory protection when handling cut foam.
Summary
Adding floor Insulation in cold‑climate homes delivers immediate comfort and long‑term energy savings. It works by reducing conductive heat loss, stopping drafts, and managing moisture. Choose materials based on R‑value, structural needs, moisture tolerance, and budget. Install with attention to air sealing and vapor control. With proper planning, this upgrade pays back financially within a few years and continues improving living quality long after installation.
Evaluate your home’s climate, budget, and moisture history. Choose the right insulation method and materials accordingly. The comfort and savings from insulating your floor will be felt immediately and appreciated season after season.
Reviewer
Ava Clark shared her input based on 6 years of working with spray foam insulation teams. Her focus on customer trust and communication helped shape key parts of this post.