Digitized Embroidery - Where Tradition Meets Cutting-Edge Technology
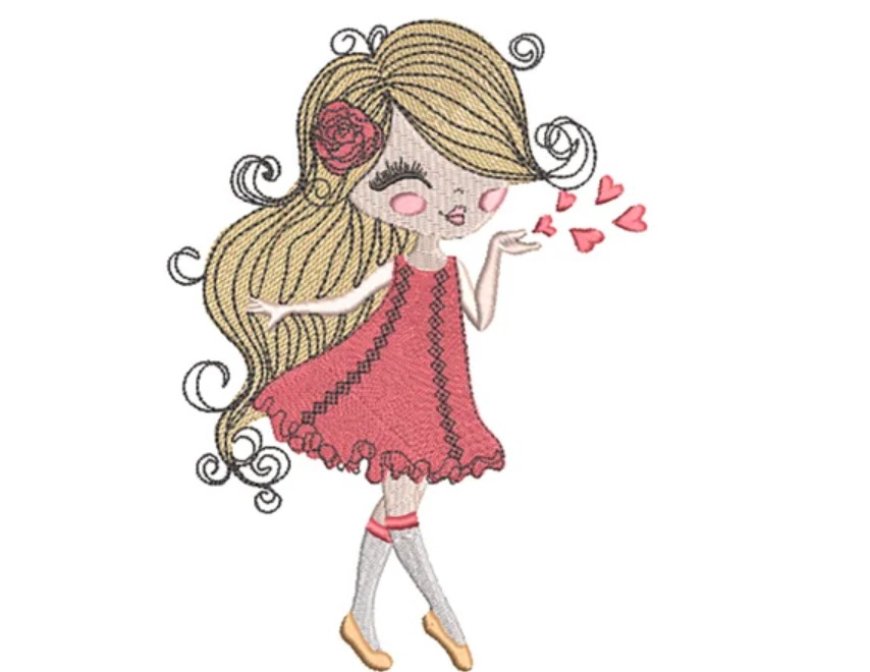
Embroidery has been decorating fabrics for centuries, with artisans painstakingly stitching intricate designs by hand. Today, that same art form has evolved into something extraordinary— digitized embroidery, where time-honored craftsmanship merges with modern technology to create stunning, precise, and customizable designs faster than ever before.
This fusion of old and new has revolutionized the textile industry, making professional-quality embroidery accessible to businesses, hobbyists, and designers alike. Whether you're personalizing a hat, branding corporate uniforms, or creating intricate artwork on fabric, digitized embroidery bridges the gap between traditional hand-stitching and the efficiency of computerized precision.
How Digitizing Transforms Embroidery
At its core, embroidery digitizing is the process of converting artwork into a digital file that an embroidery machine can read. Instead of relying solely on manual skill, specialized software translates images, logos, or text into stitch patterns—determining everything from thread colors to stitch types, densities, and sequences.
The result? Designs that stitch out with consistent perfection every time. Unlike hand embroidery, where tiny variations are part of the charm, digitized embroidery ensures uniformity—crucial for branding, mass production, and intricate detailing. Yet, despite its technical nature, the artistry isn’t lost. Skilled digitizers still make creative decisions, adjusting stitch directions, textures, and underlays to bring depth and dimension to each piece.
The Tech Behind the Thread
So, how does it actually work? The magic happens in embroidery digitizing software, where designers:
- Trace and map the artwork, defining stitch paths.
- Assign stitch types (satin for smooth edges, fill stitches for solid areas, running stitches for fine details).
- Adjust density and underlay to prevent fabric puckering.
- Simulate the design to catch errors before stitching.
Advanced programs even use AI to auto-digitize simple designs, though complex artwork still benefits from human expertise. Once the file is ready, it’s loaded into an embroidery machine, which follows the digital instructions with robotic precision, layering threads exactly where they need to be.
Why Digitized Embroidery is a Game-Changer
Speed & Scalability
Hand-stitching a detailed design can take hours or even days. Digitized embroidery slashes that time dramatically—a machine can finish a complex logo in minutes. This efficiency is a lifesaver for businesses needing bulk orders, like branded uniforms or promotional merchandise.
Precision & Consistency
Human hands can’t match the exactness of a machine. Digitizing ensures every stitch is identical, whether you’re making one piece or a thousand. That’s why industries from fashion to sports rely on it for flawless logos and lettering.
Endless Customization
Want to tweak a design? With digitized files, resizing, recoloring, or editing is just a few clicks away. Unlike traditional embroidery, where changes mean starting over, digital files let you experiment without wasting thread or fabric.
Complexity Made Simple
Some designs—like photorealistic portraits or 3D puff embroidery—are nearly impossible by hand. Digitizing software breaks down these challenges into manageable stitch patterns, unlocking creative possibilities that were once out of reach.
The Human Touch in a Digital Craft
Despite its high-tech advantages, digitized embroidery isn’t devoid of artistry. Experienced digitizers are like translators, interpreting how a design should "speak" in stitches. They make judgment calls on:
- Stitch direction (affects how light reflects off the threads).
- Pull compensation (prevents distortion on stretchy fabrics).
- Thread breaks (minimizing color changes for efficiency).
A poorly digitized file can ruin even the best design with thread breaks, puckering, or gaps. That’s why professionals blend technical know-how with an eye for aesthetics—ensuring the final product looks as good as it functions.
The Future of Digitized Embroidery
As technology advances, so does embroidery. Innovations like:
- AI-powered auto-digitizing (for faster, smarter conversions).
- 3D embroidery (adding raised textures without foam).
- Smart textiles (embedding conductive threads for wearable tech).
are pushing boundaries. Yet, the essence remains the same: transforming creativity into tangible, thread-borne art.
Embracing Both Worlds
Digitized embroidery doesn’t replace traditional methods—it complements them. Many artists combine hand-stitching with machine work for hybrid pieces that showcase the best of both. Whether you’re a purist or a tech enthusiast, there’s no denying that this blend of heritage and innovation is stitching the future of textile design.
So, the next time you see a crisply embroidered logo or a breathtaking thread portrait, remember: it’s not just a machine’s work. It’s the legacy of centuries-old craft, perfected by the precision of modern technology.